The High-Tech Valor Glass Vials Used To Deliver The Coronavirus Vaccine
As the world waits for COVID-19 vaccines, some pharmaceutical companies stand armed and ready with an exciting improvement: better vials to hold the doses. Vials haven’t changed much in the last 100 years, but in 2011, Corning decided to do something about that. They started developing an alternative glass that is able to resist damage and prevent cracks. It’s called Valor glass, and it’s amazingly strong stuff. Think Gorilla glass for the medical industry.
Traditionally, pharmaceutical vials have been made from borosilicate glass, which is the same laboratory-safe material as Corning’s Pyrex. Borosilicate glass gets its strength from the addition of boron. Although borosilicate glass is pretty tough, it comes with some issues. Any type of glass is only as strong as its flaws, and borosilicate glasses are prone to some particularly strength-limiting flaws. Pharmaceutical glass must stand up to extreme temperatures, from the high heat of the vial-making process to the bitterly cold freeze-drying process and storing temperature required by the fragile viral RNA of some COVID-19 vaccines. Let’s take a look at how Valor glass vials tackle these challenges.
Eliminating Damage and Delamination Borosilicate glass flakes float in the vial. Image via Corning Incorporated
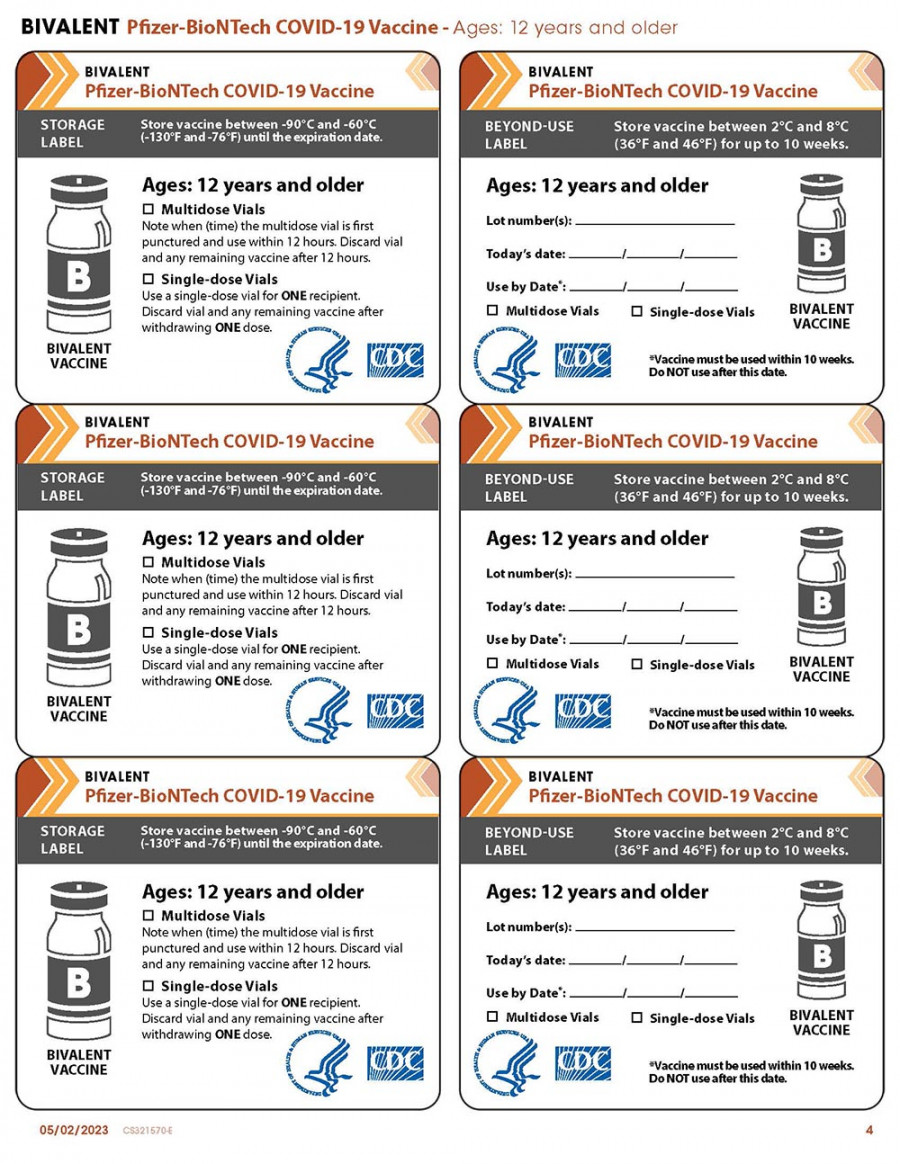
The biggest problem with borosilicate vials beyond breakage is that they are prone to delaminating internally, meaning that little pieces of glass flake off inside of the vials and contaminate the medicine. During the converting phase, where long glass tubing is separated and the ends sealed off into vials, boron evaporates from the glass network and leaves sodium borate deposits on the inside of the tube. When the vial is filled with medicine, elements like sodium, silicon, and potassium leach from the glass and into the solution.
Corning spent millions of dollars to do an in-depth study and determined that boron itself was the root cause of delamination. So after combing through the periodic table and mixing various elements with silica, they came up with a boron-free alternative that uses aluminium oxide for strength.
Vials go through several stages of production from raw glass to ready dose, and every stage presents an opportunity for damage. Batches of intravenous drugs are created during a process called lyophilization, which is a three-stage freeze-drying process. Drugs expand at different rates during the lyophilization process, and these expansions generate additional stresses within the vials.
Another problem with borosilicate glass is the dust generated on the production line. All of those vials standing shoulder to shoulder will rub together as they move down the line, generating particulates that can ruin entire batches. Valor glass has a special coating with a low coefficient of friction that reduces dust to almost nothing.

Valor vials can withstand around 1,000 pounds of force. Image provided by Corning Strong Stuff
The most impressive thing about Valor glass is its strength. In this video, a regular borosilicate vial breaks under a mere 20 kg of force. But this aptly-named super glass can withstand around 1,000 pounds force, which makes it fifty times stronger than borosilicate glass.
After the converting process that cuts and shapes the glass tubes into vials, the vials are submerged in a molten salt bath for toughness. During this process, potassium atoms in the brine swap with sodium atoms in the glass, and this fortification process is what gives Valor its strength. Corning originally developed this process for Gorilla glass — made famous through its use in scratch and shatter-resistant smartphone screens — a material which is similarly Herculean. The vials are then rinsed and coated with a polymer that greatly reduces glass dust when the bottles knock together.
To gauge the strength of the Valor vials, Corning did extensive freeze-thaw testing where they cooled vials from room temperature down to -100 °C in the span of about a minute, then allowed the vials to thaw back to room temperature over the next twelve hours. They processed and filled the vials with mannitol, a drug which expands rather aggressively during the freeze-thaw process. When mannitol crystallizes, it produces high hoop tensile stress within the vials and makes them susceptible to cracking and breakage. Valor vials are “at least 40x less likely to break than borosilicate vials under freeze-thaw conditions” (PDF) because their composition and molten salt bath help them maintain their strength throughout the lyophilization process.
Valor glass has tension layers and compression layers, and cracks that occur in the tension layer don’t propagate to the rest of the vial as they tend to do in borosilicate glasses. Valor glass will still break with enough force, so what the composition and annealing process really do is prevent cracks from growing and turning into breaks.
Over the summer, Corning received a $204M grant from the US government to expand manufacturing of Valor vials under the Operation Warp Speed initiative. And they’re not the only ones seeking new packaging solutions. Another company called SiO2 Materials Science are also producing an alternative to borosilicate that is a hybrid container — plastic lined with a thin glass-like coating that “eliminates the major concerns of glass and plastic when these materials are used alone.” Well, we need all the vials we can get.